Introduction
In the world of manufacturing and production, various processes contribute to the efficiency and quality of output. One such essential space in foundries and metalworking industries is the back casting room. Often overlooked, this specialized area plays a critical role in ensuring that casting procedures run smoothly and meet quality standards. For industries that rely on precision and high-quality metal parts, the back casting room serves as a hub for managing the critical post-casting activities.
This article provides a detailed overview of the back casting room, including its key functions, importance, benefits, and real-world applications. We will also explore the challenges that can arise in this space and offer solutions to help businesses optimize their casting operations.
What is a Back Casting Room?
A back casting room is a dedicated space within a foundry or metal casting facility where post-casting activities occur. This room is typically located at the rear of the production floor, where metal components that have already been cast are further processed, inspected, and finished. Visit here for more details allenstoneware.
The processes that take place in the back casting room include trimming, cleaning, heat treatment, and quality control. This room ensures that every part produced meets the required standards before moving to the next stage of manufacturing or assembly.
Key Functions of the Back Casting Room
- Trimming and Cleaning: After casting, excess material (also known as flash) is often present. In the back casting room, workers trim these materials off the parts to ensure a clean and precise product.
- Heat Treatment: In some cases, heat treatment is necessary to enhance the mechanical properties of the cast parts, such as strength and durability.
- Inspection and Quality Control: The back casting room is where thorough inspections take place to check for defects, cracks, or inconsistencies in the cast parts.
- Surface Finishing: Workers may apply surface treatments to improve the aesthetics or functionality of the cast parts, including polishing, painting, or coating.
The Role of the Back Casting Room in Metal Casting
The back casting room plays a pivotal role in the overall success of the casting process. While the initial casting is crucial for shaping the metal, post-casting activities ensure that the final product meets both aesthetic and functional requirements.
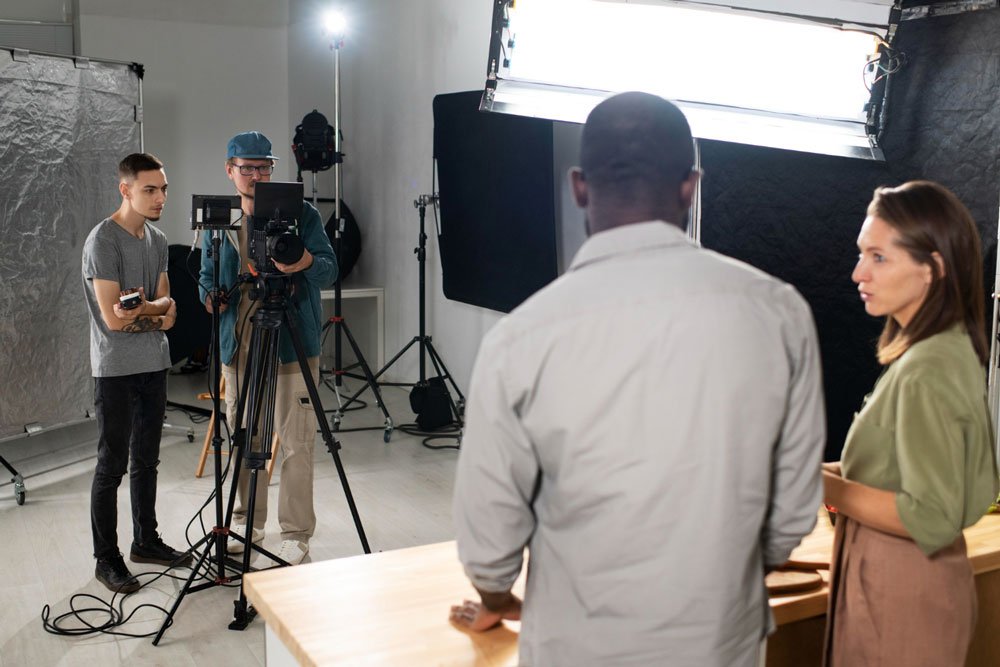
1. Ensuring Product Consistency
One of the primary responsibilities of the back casting room is to ensure that all cast components maintain consistent quality. By trimming excess materials and conducting inspections, the back casting room helps eliminate variations in the parts that could affect performance or compatibility.
2. Enhancing Durability
The heat treatment processes carried out in the back casting room significantly enhance the mechanical properties of cast parts. By improving the hardness and tensile strength of the metal, the room helps create parts that are better suited to withstand demanding environments.
3. Reducing Defects
Quality control measures in the back casting room help reduce defects before products reach the next stage of manufacturing. This step is essential for industries where precision and reliability are paramount, such as aerospace, automotive, and heavy machinery sectors.
Importance and Benefits of the Back Casting Room
The back casting room offers several critical benefits that are indispensable to foundries and manufacturing operations. By investing in a well-organized back casting room, businesses can streamline their production processes and improve the quality of their final products.
1. Streamlined Workflow
By centralizing post-casting activities in one dedicated space, the back casting room ensures that work is performed efficiently. The room is organized with specialized equipment and tools for trimming, cleaning, and inspecting cast parts, making the workflow more streamlined.
2. Quality Assurance
It is essential for maintaining quality throughout the production process. From visual inspections to advanced testing techniques, this room ensures that only parts meeting the required specifications proceed to the next stage. Consistency in quality leads to fewer rejections and returns, ultimately saving time and resources.
3. Cost-Effective Operations
A well-functioning back casting room can reduce production costs. By identifying defects early in the process, businesses can avoid costly rework and material waste. Furthermore, heat treatment and surface finishing in the back casting room can add value to the cast parts, increasing their marketability and performance.
4. Enhanced Worker Safety
It is typically designed with safety in mind. Equipped with appropriate ventilation systems, protective gear, and hazard control measures, this room minimizes the risk of accidents or exposure to harmful materials. This makes it a safer environment for workers involved in post-casting operations.
Applications and Use Cases of the Back Casting Room
It is utilized across various industries that rely on cast metal parts. Its versatility allows it to be adapted for different types of metalworking processes, making it a valuable asset in many sectors.
1. Automotive Industry
In the automotive sector, precision and durability are critical. It plays an integral role in refining cast parts such as engine blocks, transmission components, and suspension systems. By trimming excess material and conducting heat treatment, the room ensures that automotive parts are both reliable and high-performing.
2. Aerospace and Defense
Aerospace and defense companies require components with exceptional strength and accuracy. It is crucial in ensuring that parts such as turbine blades and aircraft components meet stringent safety and performance standards. Heat treatment and inspections help prevent defects that could lead to catastrophic failures in flight.
3. Heavy Machinery Manufacturing
For industries that produce heavy machinery, it is essential for creating durable, high-quality parts. Gears, axles, and other heavy-duty components benefit from the post-casting processes in this room. By improving the strength and resilience of these parts, the room helps manufacturers produce equipment that can withstand heavy use and extreme conditions.
4. Artistic Metalwork and Sculptures
In the world of artistic metalwork, it offers an opportunity to refine the details of cast sculptures and installations. Surface finishing and polishing are vital to ensuring that the final product looks aesthetically pleasing and meets the artist’s vision.
Challenges in the Back Casting Room
Despite its importance, managing it comes with certain challenges. From operational issues to maintaining consistent quality, foundries must address these challenges to ensure smooth production.
1. Equipment Maintenance
The specialized equipment used in the back casting room, such as trimming machines and heat treatment ovens, requires regular maintenance. Breakdowns can disrupt workflow, leading to production delays and increased costs.
2. Skilled Labor
Operating in it requires skilled workers who are trained in various post-casting processes. The shortage of skilled labor in the manufacturing sector can make it difficult to maintain the level of expertise needed to run the room efficiently.
3. Ensuring Consistent Quality
While it helps eliminate defects, achieving consistent quality across all cast parts can be challenging. Variations in raw materials, casting techniques, or worker performance can result in parts that don’t meet the desired standards.
4. Waste Management
Post-casting processes often generate waste materials, such as metal scraps or defective parts. Managing this waste efficiently is necessary to minimize environmental impact and reduce operational costs.
Solutions for Optimizing the Back Casting Room
Businesses can overcome the challenges associated with the back casting room by implementing certain strategies and best practices. These solutions can help improve efficiency, reduce costs, and maintain high-quality standards.
1. Regular Equipment Checks
Implementing a preventative maintenance schedule for all machinery in it can minimize the risk of breakdowns. By identifying potential issues early, businesses can avoid costly repairs and production delays.
2. Continuous Training for Workers
Ensuring that workers are continuously trained on the latest post-casting techniques and equipment can help improve performance in it. Training programs should focus on skill development, safety protocols, and quality control measures.
3. Quality Control Automation
Introducing automation in the quality control process can help maintain consistent standards across all cast parts. Automated inspection systems, such as 3D scanning and non-destructive testing (NDT), can identify defects more accurately than manual inspections.
4. Efficient Waste Recycling
To manage waste in it, businesses can invest in recycling programs that repurpose metal scraps for future use. This not only reduces environmental impact but also provides cost savings by reusing valuable materials.
Conclusion
The back casting room plays an indispensable role in modern manufacturing, particularly in industries that rely on high-quality metal components. From trimming and cleaning to heat treatment and quality control, this specialized space ensures that the final product meets the stringent requirements of various sectors. By optimizing the operations within it, businesses can improve workflow efficiency, reduce production costs, and maintain a high standard of quality.
Investing in skilled labor, regular maintenance, and quality control automation are essential strategies for overcoming the challenges that may arise in this space. By focusing on these areas, companies can harness the full potential of their back casting room and enhance their overall manufacturing process.
FAQs
1. What is the main function of a back casting room?
The primary function of it is to manage post-casting activities such as trimming, cleaning, heat treatment, and quality control of cast parts.
2. How does the back casting room improve product quality?
It ensures that cast parts are inspected, defects are addressed, and surfaces are treated to meet specific quality standards before moving on to further manufacturing stages.
3. What industries benefit from it?
Industries such as automotive, aerospace, heavy machinery manufacturing, and artistic metalworking benefit significantly from the post-casting processes conducted in the back casting room.
4. What are some common challenges in it?
Challenges include equipment maintenance, the need for skilled labor, ensuring consistent quality, and managing waste materials generated during post-casting operations.
5. How can businesses optimize the operations in it?
Businesses can optimize back casting room operations by regularly maintaining equipment, offering continuous worker training, automating quality control, and implementing efficient waste recycling practices.